La prison est un village
Haren, à deux pas de Bruxelles : un établissement pénitentiaire destiné à accueillir près de 1190 détenus émerge peu à peu du paysage. En rupture totale avec le passé car il ne ressemble en rien aux prisons que nous avions l’habitude de voir, aux bâtiments en étoile dotés d’un hall central. Le nouvel établissement est un complexe qui compte différents édifices assurant différentes fonctions pour différents occupants. Il abritera ainsi plusieurs maisons d’arrêt, une maison de peines pour hommes, un centre fermé et un centre ouvert pour femmes, un centre d’observation, un centre hospitalier et psychiatrique ainsi que des bureaux administratifs. La nouvelle prison remplacera celles de Saint-Gilles, Forest et Berkendael.
Le village pénitentiaire s’inscrit dans le cadre du masterplan « Détention et internement dans des conditions humaines ». En optant pour des bâtiments et des unités plus petits, destinés à accueillir environ 30 personnes, les pouvoirs publics entendent améliorer la qualité de vie à la fois des détenus et du personnel carcéral. « Un village fermé ayant pour mission de remettre ses habitants sur le droit chemin. »
Pour ce mégaprojet, nous avons pris rendez-vous avec l’entrepreneur et sa personne de contact au sein de notre Groupe. Gilles Geenen est responsable de la conception et chargé des grands comptes chez Denys, partenaire du consortium AM Cafasso Construction (Denys SA & FCC Construction).
Ina Jans est quant à elle en charge du bureau de dessin des préfabriqués massifs chez Prefaco.
Le défi est de taille… et la simplicité n’est pas de mise ?
Ina Jans : De fait. Avec une moyenne de 35 m³/jour, nous avons jusqu’à présent produit quelque 5700 m³ d’éléments préfabriqués en béton. Nous avons dû sortir d’usine le volume souhaité dans les meilleurs délais. C’est pourquoi le département ingénierie s’est penché en priorité sur les éléments typiques, plus répétitifs, qui pouvaient produire du volume en usine sans nécessiter trop d’efforts de la part du bureau de dessin. Il s’agissait principalement des cloisons de séparation entre cellules (doubles faces lisses) et des éléments destinés aux couloirs (une face lisse de coffrage, une face polie).
Pendant ce temps, le bureau de dessin a travaillé d’arrache-pied au développement de modèles 3D pour les panneaux préfabriqués de l’ensemble des bâtiments. Les techniques à incorporer au coulage ont ensuite été esquissées au
départ de différents fichiers ifc que nous avons reçus de l’entrepreneur, des bureaux d’études et des chargés de techniques (HVAC, électricité et sanitaires).
Pour ce faire, une étroite concertation s’est avérée nécessaire avec l’entrepreneur et les bureaux d’études. Les équipements à incorporer ne pouvaient en effet coïncider avec des raccords entre les éléments et il fallait bien évidemment que l’ensemble
réponde aux exigences techniques de stabilité concertées avec les bureaux d’études.
Après une phase de démarrage fastidieuse, chacun a progressivement identifié les priorités et desiderata des partenaires lorsqu’un problème se posait et nous sommes parvenus à tout gérer en bonne intelligence.
Le démarrage a été chaotique. Mais aujourd’hui, à quelle vitesse progressez-vous ?
Ina Jans : Tant en termes de production que de conception, nous avançons à un bon rythme : un étage complet par semaine (donc, en moyenne, 120 éléments hebdomadaires).
Serez-vous dans les temps ?
Ina Jans : Nous pouvons compter sur une solide équipe de dessinateurs expérimentés. La communication entre les différents partenaires de ce projet est cruciale. Le train doit en effet continuer à rouler et l’information doit donc circuler rapidement. Si un seul wagonnet vacille, le convoi entier risque de dérailler. Mais tout se passe à merveille. La collaboration avec l’entrepreneur est grandiose. Le bureau d’études en stabilité mérite également des louanges – lui aussi doit fournir à temps et à heure les schémas des armatures et effectuer les contrôles qui s’imposent. Dans toute ma carrière, j’ai rarement eu affaire à des projets où l’on recevait un feed-back aussi rapide de la part de tous les intervenants.
Jusqu’à présent, nous n’avons parlé que du travail de dessin et du planning serré. Mais n’oublions pas que nos usines ont aussi accompli un travail phénoménal. Car si, au bureau, nous dessinons et nous planifions, ce sont toujours les collaborateurs actifs dans nos unités de production qui doivent en exécuter la réalisation !
Fiche Technique
Propriétaire : Etat belge
Maître d’ouvrage : Régie des Bâtiments
Occupant : SPF Justice
Consortium DBFM : A.M. Cafasso Construction (Denys sa & FCC Construction)
Superficie du site : environ 15ha
Superficie de la prison : +/- 116 000 m²
Capacité : 1 190 places
Pour ce chantier, Prefaco livre :
- 45 000 m² prédalles
- 1 770 m² prémurs
- 5 890 m³ voiles et murs pleins
Pour ce chantier, d-Concrete! & Ergon livrent également
La collaboration avec l’entrepreneur est grandiose.
Une pluie de lauriers pour CRH Structural Concrete Belgium !
Gilles Geenen : Nous collaborons avec différents partenaires au sein du groupe. Prefaco fournit une grande partie des murs et cloisons ainsi que l’ensemble des prédalles et des prémurs. d-Concrete! assure la coresponsabilité de l’exécution du gros oeuvre du bâtiment logistique qui abritera tous les ateliers, la cuisine collective, la blanchisserie et tous les autres services logistiques. Nous avons également commandé des doubles poutres TT chez Ergon.
Il ne reste plus qu’à espérer que tout s’articule parfaitement.
Gilles Geenen : Nous sommes ici face à un chantier extrêmement complexe, vous pouvez me croire. Je suis moi-même en contact direct avec l’équipe Prefaco à Houthalen pour les éléments préfabriqués.
La mise en route n’a pas été facile. Il s’agit d’un projet DBFM (Design, Build, Finance & Maintain) de très grande ampleur. Son idée de base émane de notre équipe et nous sommes bien entendu responsables de l’ensemble du projet de conception et d’exécution ; nous devons dès lors être sûrs de notre fait. Quand nous avons entamé les terrassements en octobre 2018, le projet n’était pas encore tout à fait prêt, mais quand vous construisez au départ d’éléments préfabriqués en béton, tout doit être connu à l’avance.
C’est délicat, mais pas insurmontable. Nous avons commencé par dessiner les éléments-types, tous identiques. Il s’agit des cloisons de cellules, des murs de couloirs et des éléments entourant les gaines. L’ensemble du projet a été conçu suivant une philosophie BIM; nous avons donc modélisé tous les bâtiments en 3D. En recourant à de tels modèles, le bureau de dessin de Prefaco a pu esquisser les éléments à couler en 3D et en concevoir les armatures. Après contrôles, les pièces dessinées ont été approuvées puis renvoyées à Prefaco pour la mise en production. Le processus se déroule sans heurts : je suis pleinement satisfait de la collaboration avec l’équipe en place à Houthalen pour la production des éléments préfabriqués ainsi qu’avec les équipes chargées des prédalles et des prémurs à Wieze. Leurs connaissances et leur réactivité nous sont extrêmement précieuses et permettent le bon déroulement de ce chantier. Nous ne pouvons que nous féliciter de la collaboration avec CRH Structural Concrete Belgium.
Un nombre substantiel de pieux ont dû être enfoncés dans le sol.
Gilles Geenen : Au total, ils représentent plus de 50 km. Nous avons dû prévoir des pieux de fondation pour tout. Le complexe pénitentiaire est en effet bâti sur un sol de relativement piètre qualité. Nous nous trouvons ici dans la vallée de la Woluwe, où il y a toujours eu des marécages. De plus, lors des terrassements, nous sommes tombés sur une décharge historique dans la partie haute du site.
La quantité totale de béton préfabriqué pour ce projet représente pratiquement 25 000 m³. Comment parvenezvous à coordonner tout cela ?
Gilles Geenen : Oui, il faut dépenser beaucoup de temps et d’énergie pour synchroniser tous les partenaires et recevoir un retour d’information en temps utile afin que la production puisse débuter et se dérouler sans problème. Mais le mérite du résultat en revient à toute l’équipe, même si la coordination de l’ensemble des partenaires reste un défi d’envergure. Il importe toutefois de garder à l’esprit que tous les intervenants poursuivent le même but et donnent le meilleur d’eux-mêmes pour y parvenir.
Notre équipe BIM contrôle les modèles en continu. Ces derniers sont ainsi vérifiés à de multiples reprises avant d’être envoyés à nos partenaires et les modèles qui nous reviennent sont contrôlés de façon extensive avant la mise en production effective. Cela prend beaucoup de temps mais c’est essentiel pour accélérer l’examen des dessins de pièces et limiter la marge d’erreur. Et le résultat est à la hauteur : à quelques rares exceptions près, le puzzle des éléments préfabriqués s’emboîte parfaitement sur le chantier.
Quid du délai d’exécution ?
Gilles Geenen : Nous avons décroché le contrat en juillet 2018 et la date de mise à disposition est le 18 mars 2022. Nous essayons de respecter le calendrier des travaux mais quelques événements inattendus ont pesé sur le planning.
Nous ne pouvons que nous féliciter de la collaboration avec CRH Structural Concrete Belgium.
Lisez d'autres articles intéressants dans notre magazine Element.
DÉCROUVEZ NOS AUTRES RÉALISATIONS
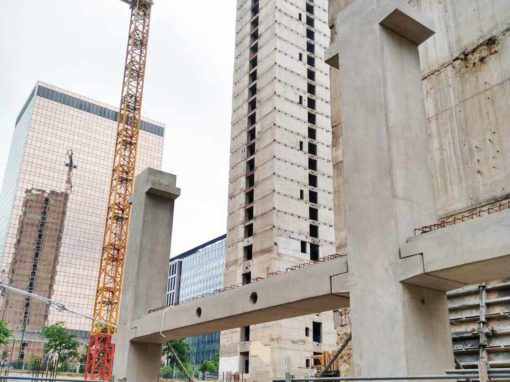
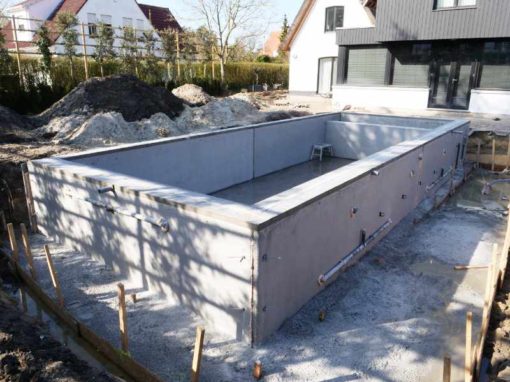
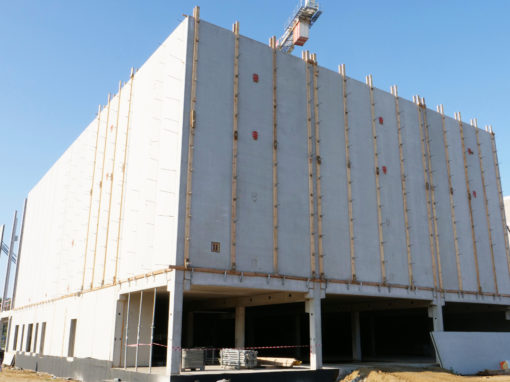
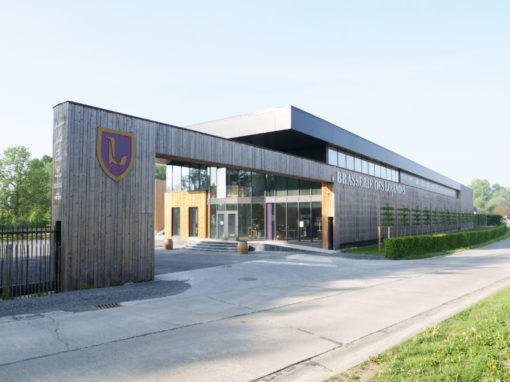
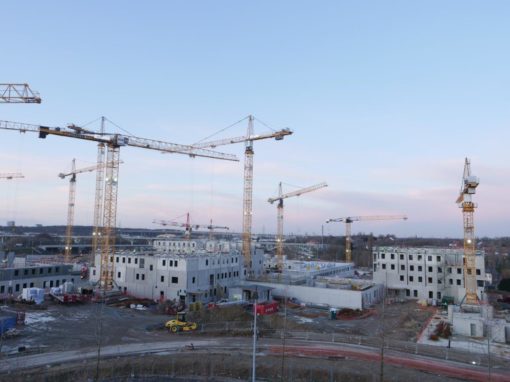
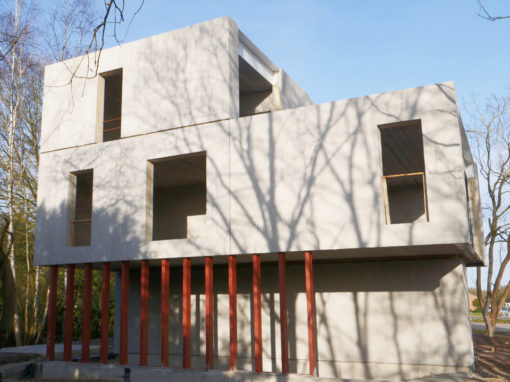
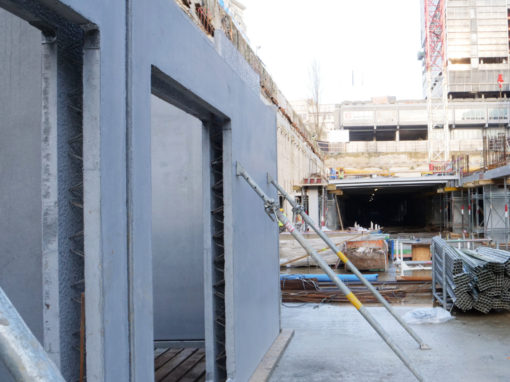
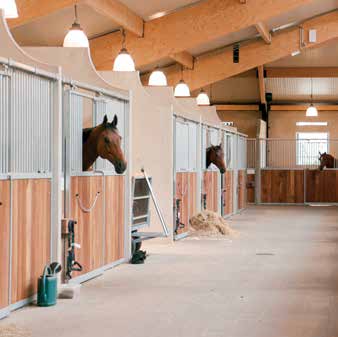
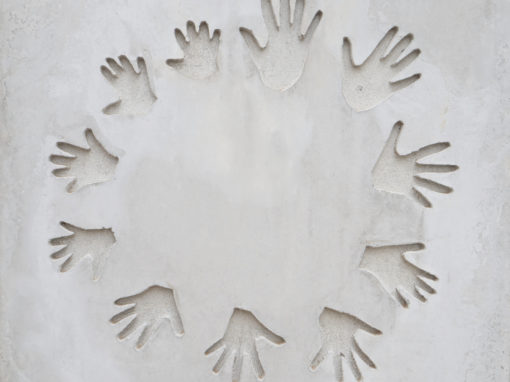
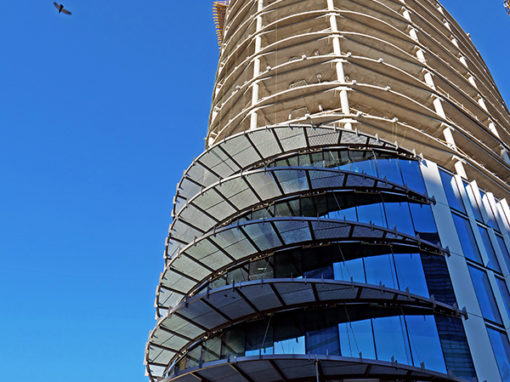
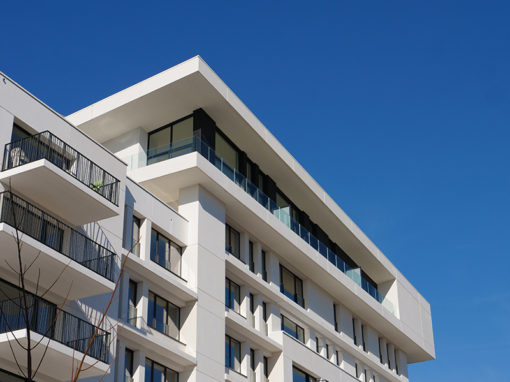
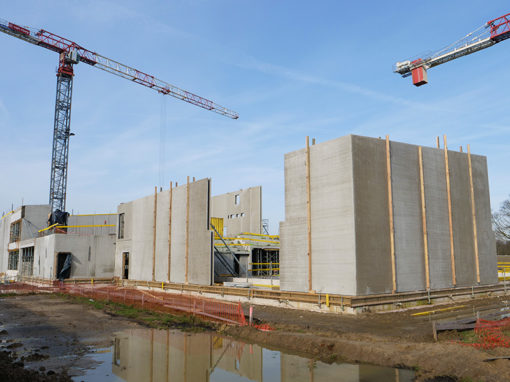
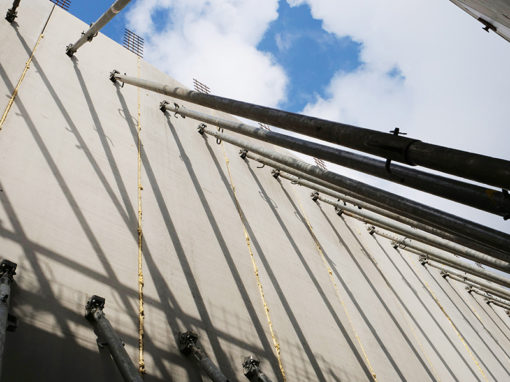

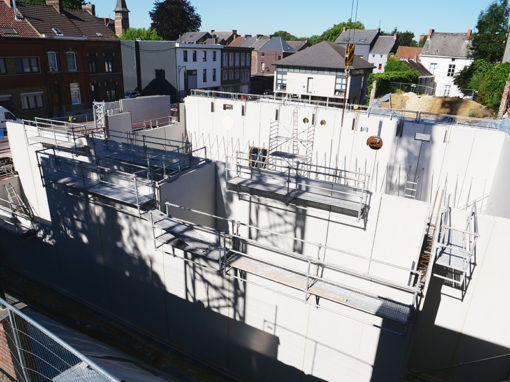
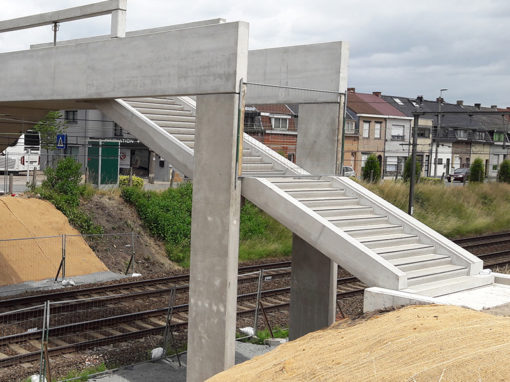
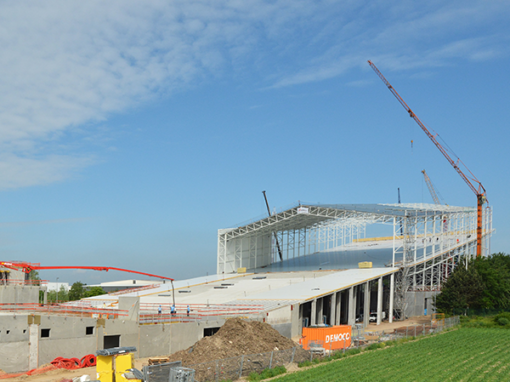
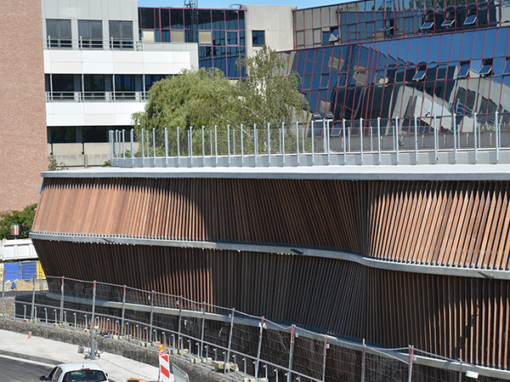
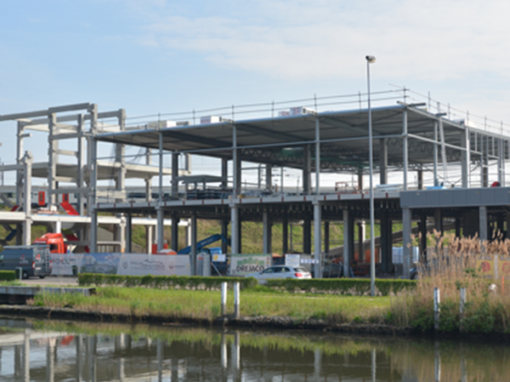
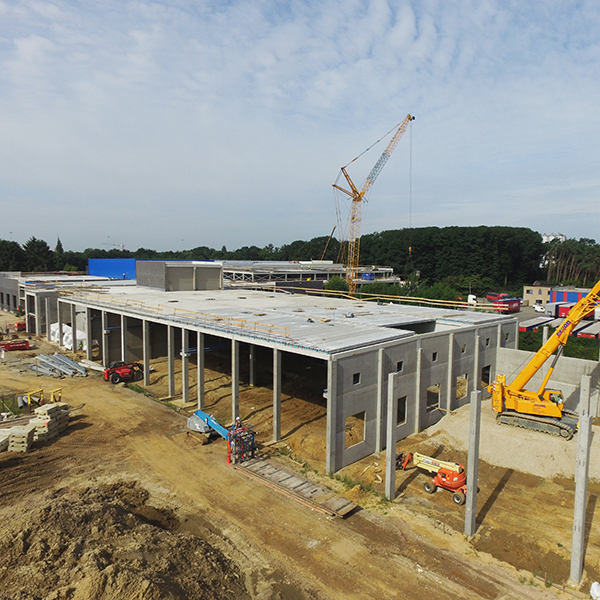
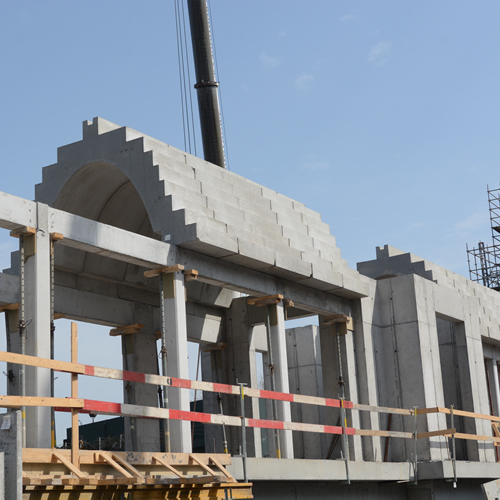


